

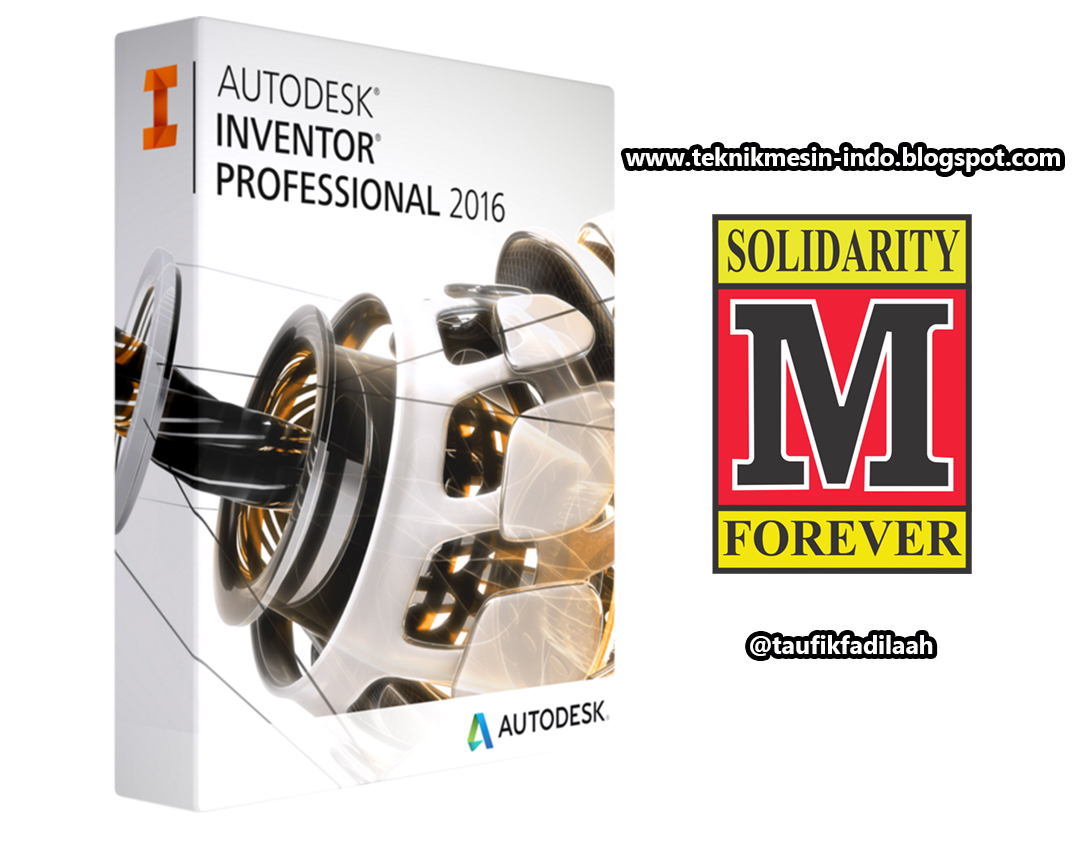
The details of analysis performed and the results obtained are discussed in this paper. This is because the ASME Section III deals with nuclear components. This means that, the pressure vessels designed by ASME Section III, give less allowable working pressure as compared to VIII-2. It was observed that the limit load predicted using ASME Section III is more conservative, than the one suggested by Section VIII division-2. Limits loads were evaluated using different methods suggested by ASME Section III and VIII-2. In the present study, non-linear finite element analyses were performed on a typical pressure vessel using two different models Viz. Both use design by analysis (DBA) method which in general is more complex, and hence needs expertise. Among these, ASME Section III and Section VIII division 2 are widely used in nuclear and general application pressure vessel design respectively. The results obtained shows that the nozzle design is safe for the design loading conditions.ĭesign of pressure vessels is governed by standard design codes that ensure high safety performances. After analysis, it is found that maximum localized stress arises at the nozzle to shell interface near the junction area. For given boundary and loading conditions, the stress developed is analyzed using mechanical workbench of ANSYS software.

A solid model, pressure vessel having nozzle is created by using Design Modeler of ANSYS program.

Div.2 has procedure for the use of Finite Element Analysis (FEA) to determine the expected stresses that may develop during operation. ASME section viii division 1 follows design-by-formula approach while division 2 contains a set of alternative rules based on design-by-analysis approach. The ASME Boiler and Pressure Vessel Code (BPVC) standards are used for the design and fabrication of boilers and pressure vessels. This paper presents the stress analysis of nozzle and shell junction of a pressure vessel.
